Optimizing Supply Chain Efficiency with Barcode Scanners
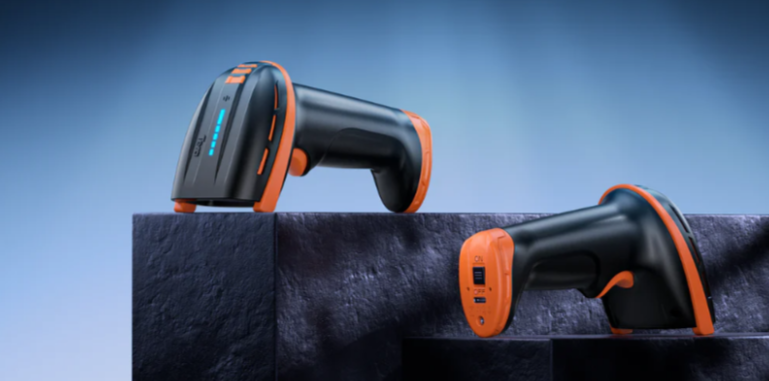
Introduction
In today’s intricate supply chain landscape, barcode scanners have become vital instruments for streamlining inventory management and enhancing overall efficiency. By incorporating barcode technology into warehouse operations, businesses can effortlessly monitor products, curtail errors, and substantially boost productivity. This technology provides real-time insight into inventory levels, minimizing stock discrepancies and ensuring seamless operations.
Understanding Warehouse Barcoding
Warehouse barcoding involves using barcodes to manage and track inventory within a warehouse. This technology is essential for streamlining operations, improving accuracy, and increasing efficiency across the supply chain. Barcode scanners are integrated into daily processes, allowing businesses to maintain real-time visibility into their inventory, reduce errors, and improve productivity.
Key Components of Warehouse Barcoding
- Barcode Labels: Each item, pallet, or storage location gets a unique barcode label, often using 2D barcodes or QR codes for easy identification and tracking.
- Barcode Scanners: Warehouse staff use barcode readers or handheld devices to scan barcode labels on items or storage locations, quickly capturing and transmitting inventory data.
- Warehouse Management Systems (WMS): WMS or Inventory Management Systems (IMS) process and store barcode data, keeping digital records of each item’s location, quantity, and other details for real-time updates and tracking.
Combining these elements provides a streamlined, accurate, and efficient method for managing warehouse operations. A well-implemented barcode system improves visibility and minimizes errors, whether managing thousands of products or a smaller inventory.
See also: The Art of Digital Magic: How Technology Transforms Entertainment
Benefits of Barcoding in Warehouse Operations
Warehouse barcoding offers significant advantages over traditional inventory management methods. Implementing barcode systems can lead to a considerable reduction in inventory errors, resulting in fewer stockouts and overstocking issues.
Real-Time Tracking
Barcode scanning offers real-time product tracking, which allows for monitoring inventory levels, making informed restocking decisions, and providing better demand forecasting. This results in faster response times to changes in demand.
Error Reduction
By automating data entry, barcode scanning minimizes the risk of human error, reducing incorrect inventory counts, stock discrepancies, stockouts, and overstocking, thus improving the bottom line.
Enhanced Efficiency
Barcode technology improves operational efficiency by enabling employees to quickly locate, scan, and update product information, reducing task completion times. This leads to increased productivity and a reduction in labor costs due to fewer manual inventory management steps.
Common Barcoding Technologies in Warehouses
Different types of barcoding technologies are used in warehouse operations, each with unique advantages and disadvantages. The right system depends on specific operational needs.
Code 39
This barcode is simple and easy to read, which makes it suitable for basic inventory management. However, it has a limited data capacity and is less effective for complex operations requiring extensive information.
Code 128
Code 128 is more versatile than Code 39 and can store more information, making it suitable for retail and distribution tasks that require detailed inventory tracking. This is suitable for both 2D and conventional linear barcodes.
Data Matrix
Data Matrix barcodes are optimal for warehouse operations that need high-density data in a small space. These barcodes can store large quantities of information, making them excellent for managing intricate inventory systems. QR codes can be used with Data Matrix for better adaptability and mobile scanning.
Selecting the right technology depends on inventory complexity and operational scale. Assessing the advantages and disadvantages of each will ensure alignment with warehouse management goals.
Choosing the Right Barcode System
Selecting the right system is essential for data capture, error reduction, and productivity. Factors to consider when choosing the barcode system include:
WMS Compatibility
Ensure the barcode system integrates seamlessly with your existing Warehouse Management System (WMS). A well-integrated system enables real-time inventory tracking for improved accuracy.
Type of Barcode Scanner
Selecting the correct barcode scanner impacts operational efficiency. Options include:
- Handheld scanners: These are portable and best suited for general warehouse use.
- Fixed-mount code scanners: These are stationary and ideal for high-volume scanning in automated environments.
- Wearable scanners: Wearable scanners offer hands-free operation, thus they are increasing efficiency in fast-paced warehouses.
Warehouse Environment
Consider the physical environment where the barcoding system will be used. Rugged barcode scanners may be necessary for harsh conditions to prevent downtime.
Cost and ROI
Evaluate the initial investment and potential ROI when assessing different systems. Weighing the long-term benefits against implementation costs is essential.
Implementing a Barcoding System
Implementing a warehouse barcoding system improves inventory management through a thorough process.
Assess Current Practices
Evaluate current inventory management processes to identify areas for improvement. This will guide how to streamline tasks with barcode technology.
Choose the Right System
Select a barcode system compatible with your WMS and warehouse environment to ensure it aligns with operational needs and supports long-term growth.
Implement Across All Operations
Apply the barcode system across the entire warehouse, including inventory management, receiving, and shipping departments, to ensure comprehensive benefits.
Employee Training
Train employees on using barcode scanners and troubleshooting common issues, which is crucial for a successful implementation. This prevents operational disruptions.
SOPs
Establish Standard Operating Procedures (SOPs) for using the barcode system to ensure consistent usage, minimize errors, and maintain inventory accuracy.
Best Practices for Barcoding
To ensure the system runs smoothly, follow these best practices.
Consistent Barcode Placement
Ensure that barcodes are placed in a uniform and consistent location on each product or pallet. This allows scanners to quickly scan labels, reducing delays and improving workflow efficiency.
Correct Scanning Distance
The code scanner must be held at the correct distance from the barcode for an accurate read. Modern scanners feature specific guides to minimize scanning errors.
Regular Maintenance
Routine maintenance and calibration of barcode equipment are crucial for optimal function. Cleaning barcode scanners and checking system functionality ensures smooth operation.
Inventory Audits
Regular inventory audits ensure that the barcode system accurately tracks products. Audits identify discrepancies between physical inventory and digital records, which facilitates necessary adjustments.
Troubleshooting Common Issues
Challenges such as scanning errors, barcode degradation, and connectivity problems can affect warehouse operations.
Barcode Scanning Errors
Inspect labels for damage or improper printing. Recalibrating the barcode scanner may also resolve accuracy issues.
Barcode Degradation
Use durable labels or protective coatings to protect against heat, moisture, or abrasion. Upgrading to 2D barcodes or QR codes may provide a better solution due to their ability to hold more data in smaller spaces and improved damage resistance.
Connectivity Issues
Check device network connections and ensure stable wireless connections. Updating or improving system communication infrastructure may be required.
Integrating with Other Systems
Integrating warehouse barcoding with warehouse management systems (WMS) and enterprise resource planning (ERP) systems optimizes efficiency. Connecting these systems streamlines data flow, which minimizes manual intervention and reduces errors.
WMS integration with barcode scanners provides real-time updates on inventory levels, location tracking, and order processing. Integrating ERP systems centralizes data, offering a unified view of supply chain operations and boosting overall efficiency.
Through integration:
- Data transfers are seamless.
- Manual data entry is minimized.
- Employee productivity increases.
- Real-time visibility is gained.
For warehouse operational success, scanner tera can further improve efficiency and accuracy.
Conclusion
Warehouse barcoding is a fundamental tool for modernizing inventory management and enhancing warehouse efficiency. Implementing a barcode system offers many advantages, like improved accuracy, real-time tracking, and reduced labor costs. By staying updated on the latest barcode technology and implementing best practices, warehouses can maintain competitiveness.